Our services
Bridging the gap between Suppliers and Customers
We’re providing an end-to-end service for businesses across the world, from entrepreneurial startups to global corporations.


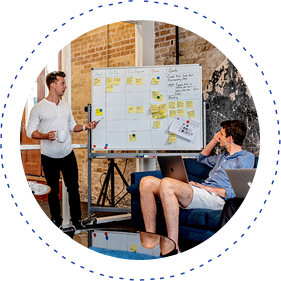
Sourcing & Product Development
From the concept and design phase to sampling and all the way through the production process, QCS handles and provides a complete solution.
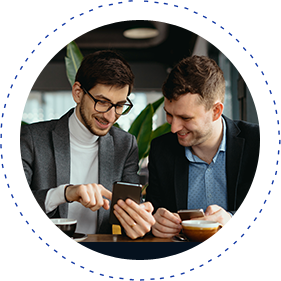
Quality Control / Inspections
Nearing the end of the production, a member of our team will do a full QC report to ensure the order is to spec and initial sampling.
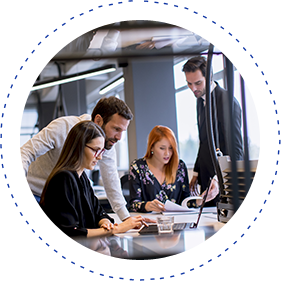
Shipping & Consolidation
Our logistics team make the whole shipping process as easy as possible. We handle all the tedious admin work and cater to your needs with all forms of freight.
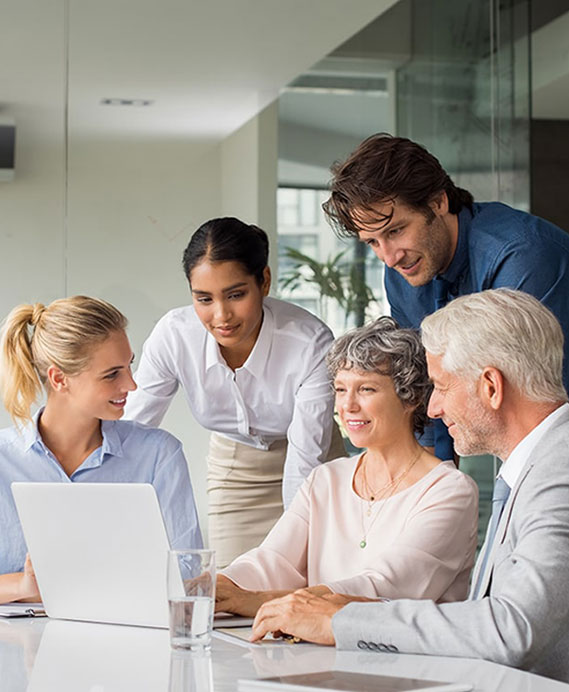
why choose us
Your one-stop sourcing company in the Asia-Pacific
Our diverse talented team work every day to provide the best service and to make our clients happy

27 Years of experience
Lorem Ipsum. Progravida nibh an sollicitudin, lorem quis bibendum auctor lorem ipsum,

Factory Direct Service
The result is a more simplified and cost-effective 'factory-direct' service – with more value to you.

Satisfaction guranteed
What makes us a leading firm is the delivery of quality and value to our clients.
explore Quality control sourcing services
Sourcing & Product Development
Sourcing Products from India similar to the existing range of Buyers/Importers.
Introducing new categories of products keeping the clients market & customers in mind.
Doing competitive sourcing from different manufacturers so that the client gets new designs, the best prices & lead times for production.
Monitoring the progress of samples development and getting them to you in time. Prototype samples received from clients are initiated.
Developments are made from the sketches, illustrations, photographs sent by the buyers.
Modifications can be made to requirement to the sample selected.
Selected/developed sample ranges are sent to the clients for review/approval.
Monitoring and giving technical support and sorting out problems on sample stages.
Order Placement.
Once the samples are approved, orders are placed with different suppliers.
Performa invoice is generated by the vendor & LC/Advance/TT request is sent through us.
LC/Advance/TT is sent by the buyer for the order placed to the vendor.
EXPLORE QUALITY CONTROL SOURCING SERVICES
Production Follow-up
Material evaluations.
Day to day monitoring and giving technical support and sorting problems on initial stages.
Order follow up with exporters for timely delivery of shipments.
Sample appraisal.
Identify and rectify production problems during placement.
Analyze quality data and co-relate results with buyers audits.
Monitor lab test results and match against local testing data.
Maintain accurate product details and records.
Labeling instructions.
Buyers are kept updated on the production progress regularly.
explore Quality control sourcing services
Quality Control / Inspections
Sample Approval – Customers either provide their own designs or they select from the range offered by the vendors. The vendors then prepare 3 counter samples for approval… one sample is sent to the buyer and upon approval, the balanced 2 samples are signed out of which one is returned to the vendor & the other is kept with us. These 2 samples are called the Master Samples, based on which production and inspection is done.
Inspections criteria- The procedures are followed for Quality Control & Inspections as per the chronology detailed below.
Initial inspection is done at the stage when the goods are produced/semi-finished and parameters like design, weight, dimension, material & quality are compared with the Master Sample.
In-line inspection is a very detailed effort, which is done at the finishing stage and the final product is inspected along with a check on packing material. All data is recorded on Inspection Sheets and re-work & technical guidance is advised, if necessary. 10%-15% of the goods are inspected during in-line inspection, which is as per AQL sampling plan. On approval of the merchandize, instructions are given for final carton packing. If any material/ finish testing is required to be carried out by any external testing agency, the same is got done and the test certificate is attached with the Inspection Sheet.
Mid-line inspection is a more detailed effort, like pre final inspection which is done at the finishing and during final packaging stage. All data is recorded on Inspection Sheets and re-work is advised, if necessary. 40%-50% of the merchandize is packed during mid-line inspection which is as per AQL sampling plan.
Final Inspection is carried out when the goods are finally 100% packed in cartons and the documents are ready for shipment. Final inspection is carried out as per AQL, as per item of the Invoice Quantity from the packed cartons. Parameters inspected indicate final packed quality as percentage of the Master Sample, packing specifications and shipping documents. On being satisfied that the shipment lot conforms to the Master Sample, all packages are sealed with carton sealing stickers and the inspected cartons are signed by the technical quality representative and all records are done on the Final Inspection/ Carton Sealing Sheet.
EXPLORE QUALITY CONTROL SOURCING SERVICES
Shipping & Consolidation
Once the final inspection has been conducted and goods are cleared we overlook to make sure that goods are handed over to the nominated consolidator f or on time shipping.
In case the buyer does not have a nominated consolidator then we help to find a consolidator & shipping line for the client. Post Shipment Document
The vendor will dispatch the original documents after receiving the balance payment.
The documents can be sent through bank or directly to the buyer as per instruction.
Original Docs – Invoice, Packing list, B/L & GSP.
We are on a never ending quest for perfection. Our ensembles are noted for their quality workmanship. Every stage of sourcing is keenly observed and undertaken as per the stringent norms. We are striving to come forth with unique styles to match international trends.
We believe in building relationships that prove to be a faithful business venture both for us as well as for the clients we are associate with. To facilitate the process of buying we are always at the service of our prospective clients from day one. We are committed to provide the highest level of service and support and to work with clients in a positive relationship, step by step.
Let’s get started your project with professional way